Many people are familiar with the haunting images of wildlife — including sea turtles, dolphins and seals — tangled in abandoned fishing nets.
The main issue behind Nylon-6, the plastic inside these nets, carpet and clothing, is that it’s too strong and durable to break down on its own. So, once it’s in the environment, it lingers for thousands of years, littering waterways, breaking corals and strangling birds and sea life.
Now, Northwestern University chemists have developed a new catalyst that quickly, cleanly and completely breaks down Nylon-6 in a matter of minutes — without generating harmful byproducts. Even better: The process does not require toxic solvents, expensive materials or extreme conditions, making it practical for everyday applications.
Not only could this new catalyst play an important role in environmental remediation, it also could perform the first step in upcycling Nylon-6 wastes into higher-value products.
The research was published today in the journal Chem.
“The whole world is aware of the plastic problem,” said Northwestern’s Tobin Marks, the study’s senior author. “Plastic is a part of our society; we use so much of it. But the problem is: What do we do when we’re finished with it? Ideally, we wouldn’t burn it or put it into landfills. We would recycle it. We’re developing catalysts that deconstruct these polymers, returning them to their original form, so they can be reused.”
Marks is the Vladimir N. Ipatieff Professor of Catalytic Chemistry at Northwestern’s Weinberg College of Arts and Sciences and a professor of materials science and engineering at Northwestern’s McCormick School of Engineering. He also is a faculty affiliate at the Paula M. Trienens Institute for Sustainability and Energy. Northwestern co-authors include Linda J. Broadbelt, the Sarah Rebecca Roland Professor of Chemical and Biological Engineering and senior associate dean of McCormick, and Yosi Kratish, a research assistant professor in Marks’ group.
From clothing to carpet to seat belts, Nylon-6 is found in a variety of materials that most people use every day. But, when people are done with these materials, they end up in landfills or worse: loose in the environment, including the ocean. According to the World Wildlife Federation, up to 1 million tons of fishing gear is abandoned in the ocean each year, with fishing nets composed of Nylon-6 making up at least 46% of the Great Pacific Garbage Patch.
“Fishing nets lose quality after a couple years of use,” said Liwei Ye, the paper’s lead first author who is a postdoctoral fellow in Marks’ laboratory. “They become so water-logged that it’s difficult to pull them out of the ocean. And they are so cheap to replace that people just leave them in the water and buy new ones.”
“There is a lot of garbage in the ocean,” Marks added. “Cardboard and food waste biodegrades. Metals sink to the bottom. Then we are left with the plastics.”
The greenest solvent is no solvent
Current methods to dispose of Nylon-6 are limited to simply burying it in landfills. When Nylon-6 is burned, it emits toxic pollutants such as nitrogen oxides, which are linked to various health complications including premature death, or carbon dioxide, an infamously potent greenhouse gas.
Although other laboratories have explored catalysts to degrade Nylon-6, those catalysts require extreme conditions (such as temperatures as high as 350 degrees Celsius), high-pressure steam (which is energetically expensive and inefficient) and/or toxic solvents that only contribute to more pollution.
“You can dissolve plastics in acid, but then you are left with dirty water,” Marks said. “What do you do with that? The goal is always to use a green solvent. And what type of solvent is greener than no solvent at all?”
Recovering building blocks for upcycling
To bypass these issues, the researchers looked to a novel catalyst already developed in Marks’ laboratory. The catalyst harnesses yttrium (an inexpensive Earth-abundant metal) and lanthanide ions. When the team heated Nylon-6 samples to melting temperatures and applied the catalyst without a solvent, the plastic fell apart — reverting to its original building blocks without leaving byproducts behind.
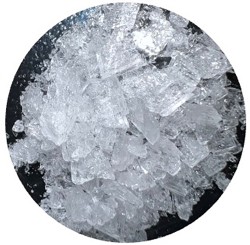
Recovered monomers from the catalytic process.
“You can think of a polymer like a necklace or a string of pearls,” Marks explained. “In this analogy, each pearl is a monomer. These monomers are the building blocks. We devised a way to break down the necklace but recover those pearls.”
In experiments, Marks and his team were able to recover 99% of plastics’ original monomers. In principle, those monomers then could be upcycled into higher-value products, which are currently in high demand for their strength and durability.
“Recycled nylon is actually worth more money than regular nylon,” Marks said. “Many high-end fashion brands use recycled nylon in clothes.”
Efficiently targeting Nylon-6
In addition to recovering a high yield of monomers, the catalyst is highly selective — acting only on the Nylon-6 polymers without disrupting surrounding materials. This means industry could apply the catalyst to large volumes of unsorted waste and selectively target Nylon-6.
“If you don’t have a catalyst that’s selective, then how do you separate the nylon from the rest of waste?” Marks said. “You would need to hire humans to sort through all the waste to remove the nylon. That’s enormously expensive and inefficient. But if the catalyst only degrades the nylon and leaves everything else behind, that’s incredibly efficient.”
Recycling these monomers also avoids the need to produce more plastics from scratch.
“These monomers are produced from crude oil, so they have a huge carbon footprint,” Ye said. “That’s just not sustainable.”
What’s next?
After filing a patent for the new process, Marks and his team have already received interest from potential industrial partners. They hope others can use their catalysts on a large scale to help solve the global plastic problem.
“Our research represents a significant step forward in the field of polymer recycling and sustainable materials management,” Ye said. “The innovative approach addresses a critical gap in current recycling technologies, offering a practical and efficient solution for the nylon waste problem. We believe it has implications for reducing the environmental footprint of plastics and contributing to a circular economy.”
To help bring the discovery to others, Kratish is working with the Querrey InQbation Lab, Northwestern's technology accelerator.
"I firmly believe that true impact is realized when transformative ideas are not only conceived but also brought to the market," said Kratish, who is a 2023 Querrey Entrepreneurial Fellow. "Our progress with this study brings us one step closer to translating these insights into a technology ready to make a lasting impact worldwide. As part of this commitment, I've initiated the journey to commercialize this technology, marking the next crucial phase in our mission to revolutionize Nylon-6 recycling."
The study was supported by RePLACE (Redesigning Polymers to Leverage A Circular Economy), funded by the Office of Science of the U.S. Department of Energy and the National Science Foundation. Additional support came from the Institute for Catalysis in Energy Processes, which is a major research project within the Center for Catalysis and Surface Science at the Paula M. Trienens Institute for Sustainability and Energy.